Accidents at work, especially if involving fatalities, continue to be reported widely in local, regional and national media. While those on a larger scale, and sometimes accompanied by a greater level of notoriety, such as the Bangladesh building collapse in April 2013, tend to have intense international coverage and scrutiny.
In a wide range of health and safety legislation and guidelines, a duty of care applies both to employers and employees for the safe operation of workplace equipment. Such equipment, machinery or plant must be maintained and fit for purpose, the working environment should be safe, suitable training should be undertaken, operating procedures should be rigorous and relevant personal protective safety equipment should be provided and used. Accidents tend to occur when one or more of these tend not to be observed.
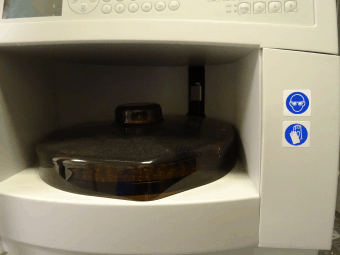
Our range of health and safety labels can assist in identifying risks and hazards at work and prohibited activities, promote employee welfare, and to indicate the use of personal protective equipment (PPE).
Potential hazards can be clearly identified. These can include electrical, biological, radiation, temperature (high, low or hot surfaces), chemical (such as toxic, corrosive, harmful or irritant), and mechanical (pinch points, moving blades, finger trap, or crush) risks in the workplace.
Mandatory labels emphasise the need to use the protective equipment supplied to prevent injury to eyesight, hearing, face, fingers, hands, body or feet. Also, others cover the need to read the manual or handbook for the equipment or for greasing or lubrication points on equipment.
Prohibition stickers advise of actions which may be dangerous, such as reaching over or into equipment, or from smoking or use of naked flames.
For further information on these safety labelling stickers, our comprehensive product ranges can be located in the following label categories; warning symbol labels; engineering labels; safety labels; laminated safety labels; custom safety labels; and Ansi labels.