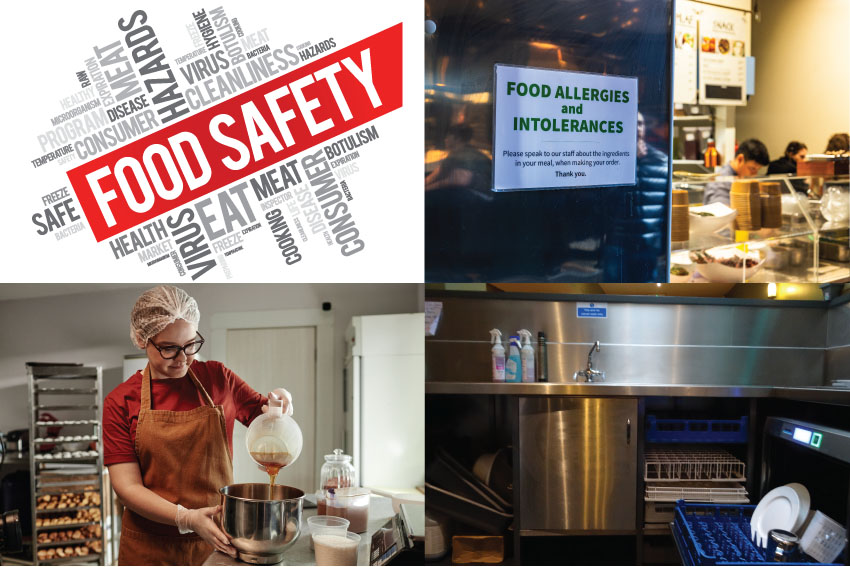
Safety and hygiene should be a top priority for any kitchen, but especially so when it comes to commercial settings. From busy restaurants to hotel kitchens, following safety kitchen rules is necessary for both safeguarding customers, and maintaining compliance.
Kitchen safety signs are one of the most effective ways to encourage this; they can range from allergen warnings and handling instructions to preparation procedures, and even bans (‘No smoking, food preparation area’).
In this article, we discuss how to label food in a commercial kitchen through a brief overview of kitchen safety signs and their meaning. More...
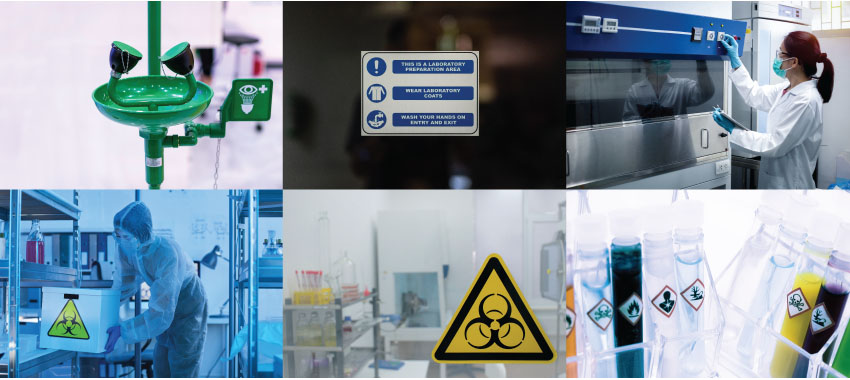
Alongside being the origin of discovery and innovation, laboratories are also home to many potential hazards along the way. Whatever the scientific field, it doesn’t come without risks – from radiation and biohazards to chemical exposure or even electrical danger.
This is why such environments need to be equipped with lab safety warning symbols as part of the compulsory measures taken to protect researchers, students, and other personnel.
Here, we talk more about lab safety rules and the importance of safety signs in the lab, before breaking down laboratory symbols and their meanings. More...
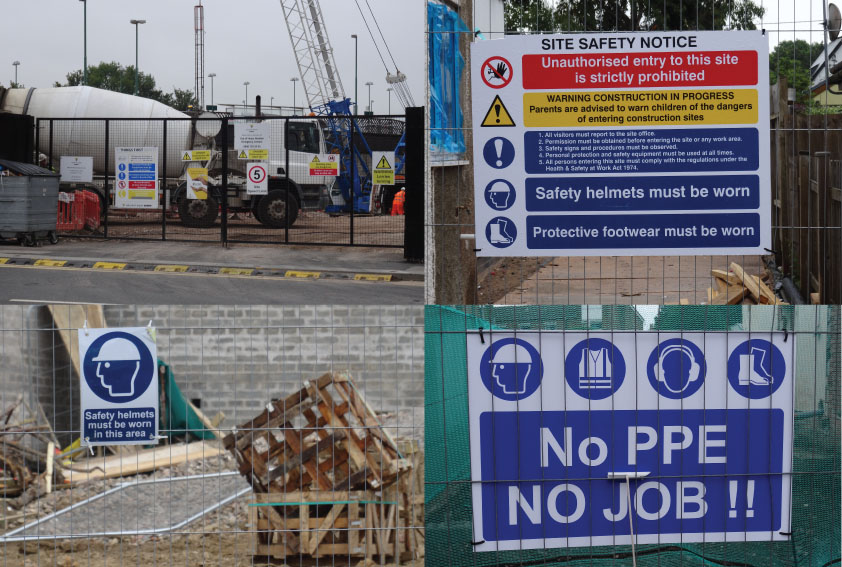
As working environments go, construction sites are among the most dangerous. Workers are regularly exposed to all sorts of hazards, ranging from electrical risks to falling debris. That’s why warning signs for a construction site are crucial to legal compliance and employee safety.
In this guide, we cover what signs are required on a construction site and best practices when it comes to displaying these. More...
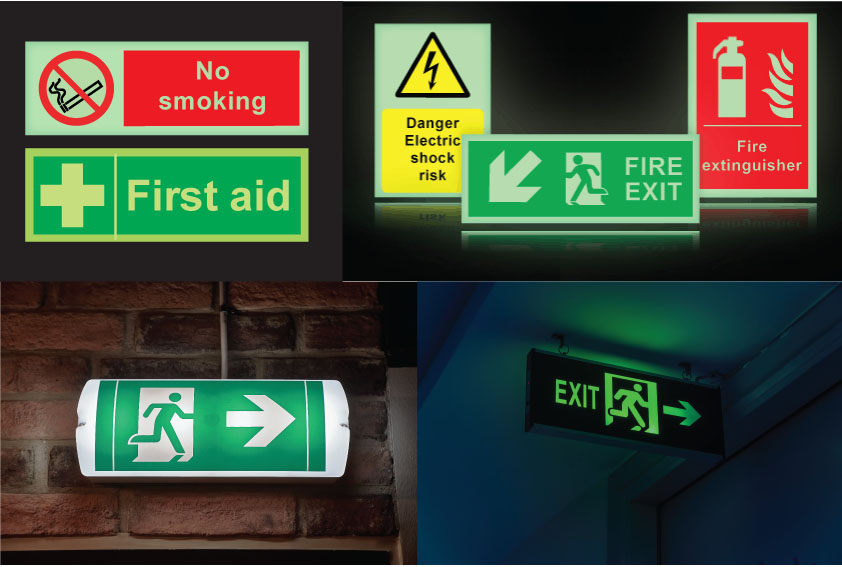
More than simply being an annoyance, power outages can become a real hazard, especially in areas which have convoluted layouts, increased foot traffic, or dangerous materials.
In the interest of efficient evacuation and quick response in case of emergency, building managers should ensure good visibility during a power failure, no matter if they’re in charge of a commercial building, office, warehouse, or laboratory.
Photoluminescent safety signs, which can be seen clearly in the dark, are a key element of that. Here, we’ll outline the essential signage each building needs, any specific regulations, and the unique requirements for certain building types. More...
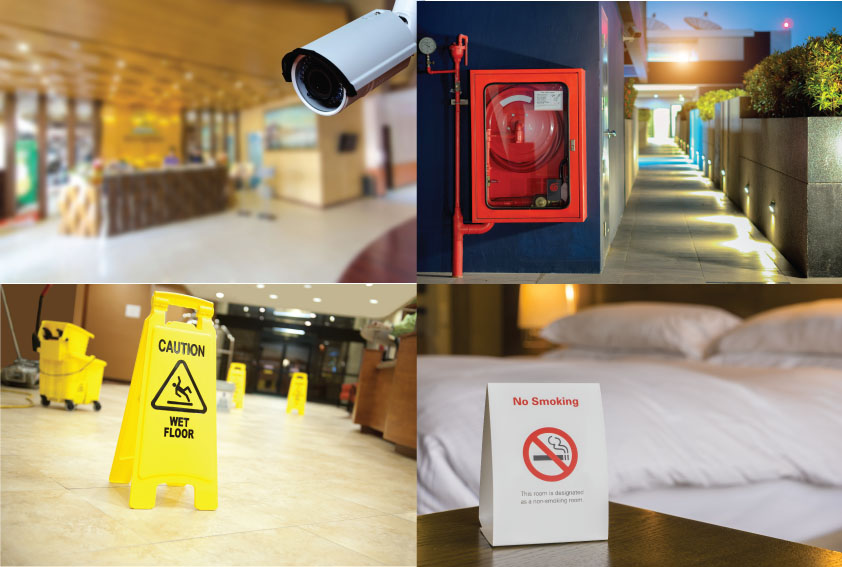
From boutique hotels to bustling resorts and everything in between, all hospitality venues need to follow hotel signage guidelines. The benefits of this are twofold – clear signs improve the guest experience for visitors, while also ensuring safety and compliance with legislation such as hotel fire safety regulations in the UK.
We’ve rounded up the essential hotel safety signs you should have to tick all the boxes for visitor safety, compliance, and guest experience. More...