No one expects an accident to happen at work, and yet there were 622,000 workplace accidents that caused injuries between 2014-2016. With this costing employer over one billion pounds, it’s in everyone’s best interest to take health and safety in the workplace seriously. If workplace health and safety is something that you feel needs improving, whether you are an employer or employee, it’s worth encouraging.
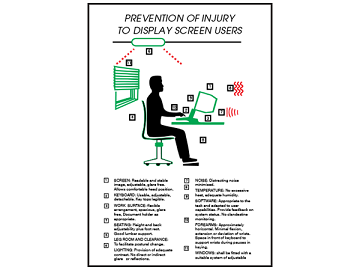
Whether you’re working on a construction site or in an office, there should be health and safety measures in place to help minimise the risk of any workplace injuries, and those in place in case an accident does occur. This will be different between work environments, but it can be as simple as knowing where the first aid box is kept and where each fire exit is.
Here are some tips for improving health and safety in the workplace:
Start at the Beginning
Make sure every new-starter is taught about what health and safety measures are in place. Whatever your work environment, knowing this information is vital. Give each employee a tour of the workplace explaining the usual fire safety protocols and paying particular attention to any hazardous areas employees should be aware of.
Offer a Refresher Course
At the same time, make sure your current employees have the opportunity to be reminded of the health and safety measures in place. This should include anything new that may have been introduced since they started, such as if anyone is a first aider, etc.
Be Prepared
Do your employees have the right PPE? If they are expected to do any manual labour (even if it's not often), have they had the appropriate training? Are there any restricted areas to be avoided? Being prepared can really make a difference – being prepared for work means you are aware of any health and safety situations that may come up.
Install Correct Labels and Signage
Even if you think employees have a good idea about health and safety, signage can drastically improve how aware people are in the workplace. Not only do these make people who are unfamiliar with the workplace aware of any hazards, it also reminds any employees to be vigilant. To have a look at our range of safety signs, click here.
Improving health and safety in the workplace doesn't have to be complicated or expensive, but is always a necessary way of keeping everyone safe. For any advice on what you may need to improve your workplace safety, feel free to get in touch. We can help you select from a massive range of health and safety signage. Call us today on 0800 3761 693.
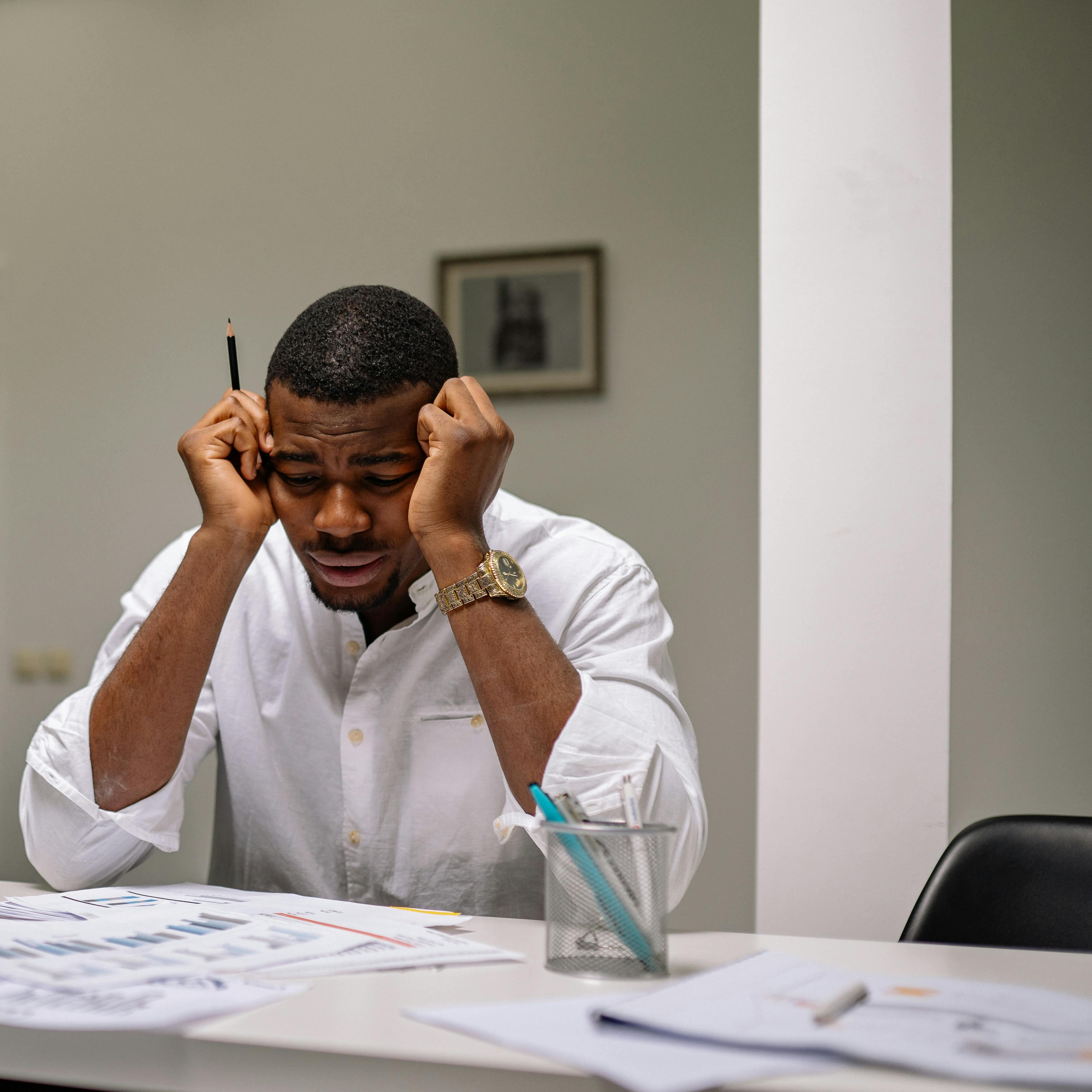
We're always talking about workplace health and safety on this blog, but most of the news stories we look at concern physical injuries: severed fingers, broken bones, that sort of thing.
However, stats suggest that the greatest threat to the health and safety of Britain's workers is not rotating blades, slippery surfaces, unprotected edges, or anything like that.
According to the Trades Union Congress (TUC), which surveyed roughly one thousand health and safety representatives across the UK, the main concern for this country's H&S officials in 2016 was... stress! More...
A few days ago, it emerged that Tata Steel had been fined over £2m, after two serious incidents occurred at its Northamptonshire site. Both of these involved workers sustaining severe hand injuries, as a result of avoidable contact with dangerous machinery.
The first of these incidents involved a 26 year old worker, who lost the middle and ring fingers on his left hand, after trying to clear a blockage on a manufacturing line with unsuitable guarding. The second incident occurred in 2015, when a 52 year old lost part of his little finger after it became caught in a lathe, again, due to unsuitable guarding on the machinery.
Although a spokesman for Tata was quoted as stating that health and safety is the company's most important priority, serious questions must be raised after two near identical incidents took place within months of one another, on the same premises no less! It is clear from the evidence found upon inspection by the HSE, that there was an obvious neglect of duty in terms of properly identifying the serious risks posed to Tata workers, as well as a failure to resolve this issue after the first incident occurred.
It shouldn't take a serious injury or fatality to make a company take their health and safety procedures seriously, and one would hope that it wouldn't take multiple incidents for a company to implement serious changes. Perhaps the only consolation going forward, is that other companies will be struck by the severity of the issue, and therefore implement better prevention strategies in their own workplaces.
For anyone concerned with avoiding the mistakes made by Tata, remember to follow a simple but impactful health and safety strategy:
- Educate - Ensure that staff are thoroughly trained before operating dangerous machinery, or performing hazardous tasks without supervision.
- Inform - Make staff aware of the risks involved in their operations, displaying safety signs and warnings to keep the message fresh in people's minds.
- Protect - Ensure that the correct safety features are in place to minimise potential risks, and provide the required personal protective equipment.
- Asses - Regularly evaluate the level of safety in your workplace, and identify any potential risks that require preventative action.
For more health and safety news and advice, follow us on Twitter, Facebook & Google+
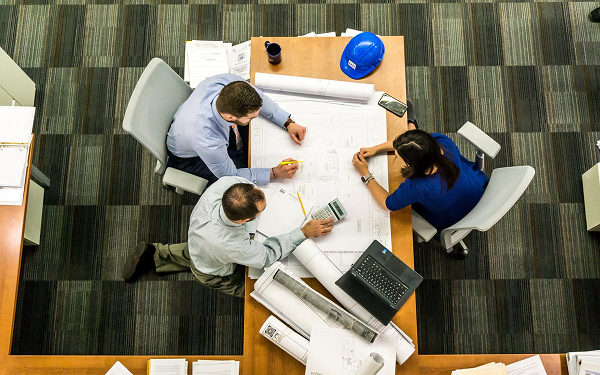
The Safety Signs and Signals Regulations act of 1966 states that there are specific mandatory signs required in the workplace, depending on the equipment and health and safety risks present in your workplace. Label Source has an extremely sophisticated range of Mandatory Safety Signs on offer. All of our prohibition mandatory health and safety signs for the workplace are produced to UK, EU and international standards ISO EN 7010.
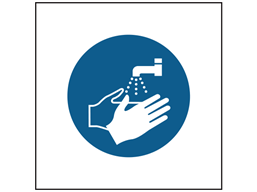
Wash your Hands Symbol Safety Sign
Our range of mandatory signs for the workplace aim to dictate actions to be taken or appropriate behaviour to be executed in the face of any health and safety risks in the workplace. Our signs will increase health and safety risk prevention and are consequently extremely important to consider - as well as being mandatory, of course.
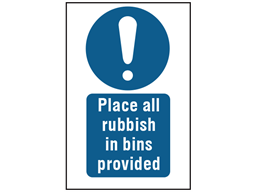
Place all Rubbish in Bins Provided Symbol and Text Sign
All our mandatory health and safety signs consist of a blue circle with a white pictogram and text panels of white text on a blue background which is clear enough to be seen in the workplace. The categories for our mandatory signs include the use of equipment including general mandatory safety signs, personal protective equipment (PPE), utilities service mandatory safety notices, manual handling mandatory signs and warning labels, fire action and kitchen safety.
Displaying the correct mandatory safety signs in the workplace not only displays your commitment to the health and safety of your staff, customers and the general public, but also ensures that anyone who enters your premises is fully aware of the health and safety standards expected in your workplace. To ensure that your business complies with the correct work and safety-related legislations then get your mandatory safety signs from Label Source today!