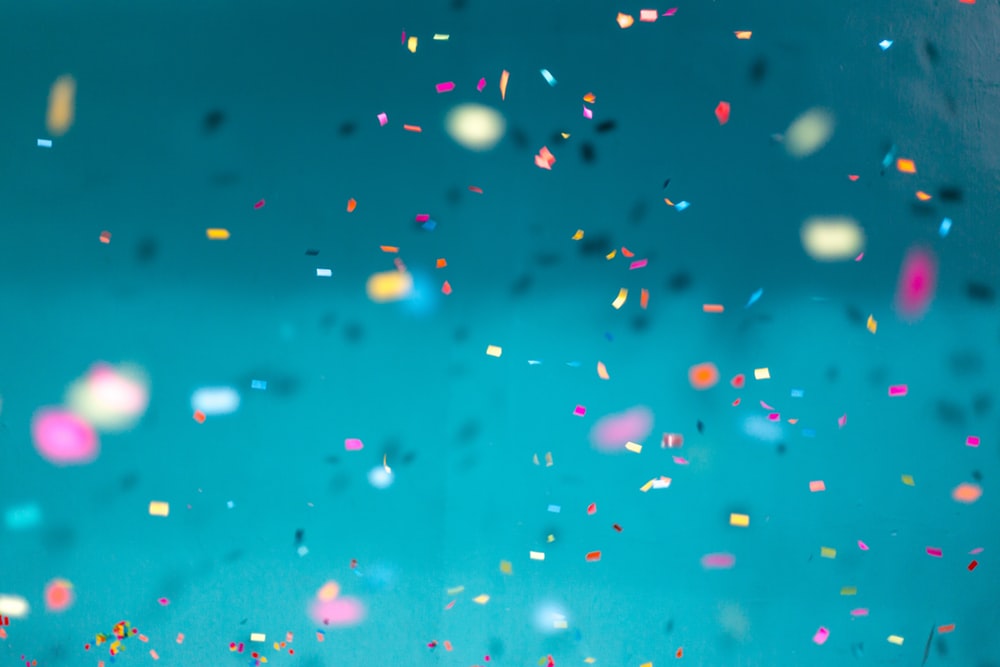
After 25 years of trading and being an authoritative voice in the ever-changing world of labels, Label Source director Colin Penfold reflects on the company’s journey and how its expertise, reach and knowledge in the industry has grown.
Label Source was formed as a limited company in September 1994, although it had been trading for two years prior to that. We had previous experience of supplying ranges of labels, signs, tapes and tags from a catalogue (as this prior to the growth of online sales on the internet). The key objective was to provide a wide selection of products in low quantities of issue to service the UK market primarily. The market place is very diverse ranging from Government Departments, NHS, Manufacturing, Education (Universities, Colleges, Schools), Construction, Facilities Management to name but a few.
Bill George, who ended up as MD of that company, joined Label Source afterwards and worked with us until his retirement last year. So between us we had over 50 years’ experience in the industry.
The aim was to select the most cost-effective method of manufacture, rather than being constrained by in-house print capacity, where efforts are sometimes used to try and fit work on machines, which they are totally unsuited.
Besides offering ranges of products to British, EU and international requirements for standard format products, another element was to provide a custom printing service, where technical advice would be given on the suitability of products so that they were fit for purpose.
An inhibiting factor in the early years was the amount and frequency of catalogues issued compared with some of our larger competitors, although many had a much more limited range of products with a concentration on health and safety signs only.
Our products are manufactured by various print processes including hot foil, screen, flexographic, letterpress, digital printing, chemical etching, laser and rotary engraving and metal pressings.
Materials are varied including synthetic pressure-sensitive films, such as vinyl, polyester, polypropylene, security materials, rigid and semi-rigid plastics, metals (anodised aluminium, brass, stainless steel in different grades), internal and external engraving laminates.
The major factor to give parity against large competitors was the advent of the internet, and particularly when shopping carts were introduced. We are now on our fifth generation website, and the last four have operated with shopping carts. These have become more sophisticated over the years, although many of the key factors have remained fairly consistent in the last 10 years, there have been trends towards more mobile purchasing.
There have been developments, especially on adhesive technology, with the introduction of super-adhesives, the improvements in availability of material substrate choice (particularly in digital printing), and laminates.
Key product types include asset marking tags, health and safety signs to latest ISO regulations, pipeline marking tapes, labels and tags, equipment marking including CE standards, quality and calibration labels and tags.
As for myself, I initially began work with AB Electronics, the Irish Export Board and BT. At BT, I was the Marketing Manager for the Label Centre, part of the BT Manufacturing Group, for six years. Here, my expertise in the industry of labels grew with my experience. As part of this job, I helped supply British Telecom, the Post Office and other organisations with several label catalogues, including safety signs. My experience at BT gave me the expertise to flourish at Label Source, as well as the industry knowledge to help make it what it is today.
Looking back, 25 years have flown by, and we’re excited to see how the industry will change going forward!
As always, if you need anything from the world of labels, check out our range and be sure to follow us on Facebook and Twitter.