We share a lot of health and safety stories on this blog, many of which focus on the news that yet another organisation has been prosecuted and fined for poor safety practices. More often than not, these law-breaking companies are in high-risk fields like construction and industrial manufacturing, and they're caught out because a worker suffered an injury (or worse) that would have been prevented had the proper regulations been observed.
Today, however, we'd like to share a news story which demonstrates that every company in every industry must abide by the rules or face the consequences. Earlier this week, The Enquirer reported that a business in Essex had been fined £20,000 for a number of unsafe practices. So what type of business was this? An engineering firm? A large factory?
No and no; in actual fact, it was the Crown Café in Southend-on-Sea. Last week, Southend Magistrates Court found the business guilty of the following food hygiene / health and safety breaches:
- No wash basin exclusively designated for hand washing in the kitchen
- No documented food safety management system
- Failure to maintain electrical installations in the café
These issues were documented during an inspection of the café in August 2015. Inspectors issues three Improvement Notices, but a follow-up inspection one year later found that the Notices had not been acted upon and that the problems were still there. As a result, Ms De'Ath was ordered to pay £1,440 (plus £1,000 in costs), and the business itself was fined £16,000 (plus £2,162.50 in costs). On top of that, Ms De'Ath and her business had to pay a victim surcharge totalling £188.
After the sentence had been delivered, a local councillor made the following statement:
"We hope this successful prosecution sends out a clear message to food businesses that you must take your responsibilities for food hygiene and health and safety seriously...we will take any action necessary to protect the public from harm."
Health and safety is a crucial concern for all organisations across all sectors. No matter what products or services you provide, it is your responsibility as a business owner to carry out a full risk assessment and take any measures necessary to minimise the risk that someone will come to harm on your premises or as a result of your operations. If you work in the food industry, then hygiene should of course be a key priority, but you are also bound by the same general health and safety legislation as any other commercial organisation. Don't let yourself end up in court like the owner of the Crown Café!
Here at Label Source, we stock a number of signs and notices to help promote hygiene and safety in a kitchen environment. Click here to browse our Kitchen Safety Signs range.
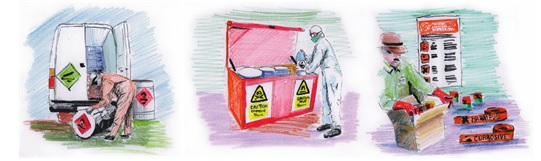
In order to protect employees and members of the public from harm, it is vitally important that chemical hazard labels are used by businesses who deal with potentially harmful chemicals.
Whatever the point of contact may be, it is paramount that the proper warnings are provided for substances which possess any of the following, hazardous qualities:
- Flammable, explosive or oxidising - Substances which present significant risks of when stored in certain conditions, or exposed to certain substances.
- Toxic - Substances which present a risk of contamination or poisoning.
- Corrosive - Chemicals such as acids, which are able to cause damage to human skin and other materials they come into contact with.
- Gases Under Pressure - Gases stored in compression containers, which present a risk of releasing the gas contained at a rapid rate if damaged.
& more, including irritants, and substances which may harm the environment.
In order to prevent damage and injury due to these risks, chemical hazard labels should be used at each point of potential contact, in order to ensure that the warnings are maintained at all times.
Chemical Hazard Labels should be used:
- In workplaces with hazardous chemicals present, such as laboratories and hospitals.
- On containers which are being used to store and transport hazardous goods.
- On vehicles which are used to transport potentially dangerous chemicals.
- During the production and packaging of substances.
If your business deals with potentially harmful chemicals, which have the ability to impact the health and well-being of those who may come into contact with them, then be sure to use chemical hazard labels and signs! These are needed to provide effective warnings of the risks connected with these substances, and instructions for dealing with the substances.
Our full selection of dangerous chemical labels has labels to suit a wide variety of purposes, and can be found here.
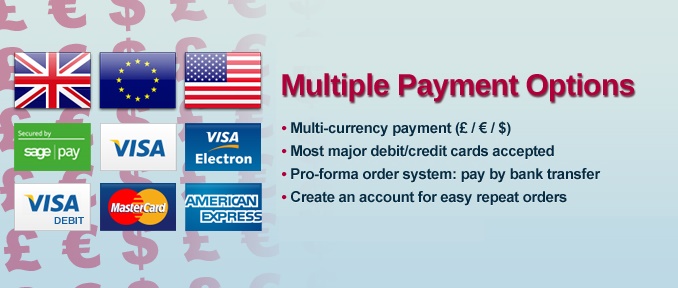
Here at Label Source, we aim to provide a flexible service that meets each and every customer's needs, whatever they may be. This means offering a huge variety of bespoke labelling options and enabling you to add your own corporate branding to our products, but it also means doing whatever we can to make the ordering process itself as smooth and as easy as possible for you.
We cater to a vast range of businesses and individuals in the UK, Europe, and even further afield. This has taught us that different customers in different countries tend to have different preferences at the checkout: some are content to simply enter their card details, while others require a pro forma invoice. Some are keen to complete the purchasing process as quickly as possible; others will take the time to register an account if it will make life easier next time around. And, of course, everyone works in different currencies depending on when they're based.
Our online store aims to cater to all of these contrasting requirements and preferences. When you place an order with labelsource.co.uk, you can:
- Choose to pay in pounds, euros, or US dollars
- Pay by credit or debit card (we accept most major card providers, including Visa, Mastercard and American Express)
- Use our pro forma order system and pay by bank transfer
- Register a Label Source account for easy repeat orders, or use our express checkout option if you're in a hurry
We're here to provide the perfect solution to your organisation's tagging, labelling and signage needs. Click here to return to our homepage and begin shopping, or contact us today if you have any questions for the Label Source team.
It has never been more important for businesses to select stock, speedily and accurately, to meet the customer expectations when expediting their orders. Therefore, it makes sense that stock locations are clearly marked, whether this be in a distribution centre, warehouse or stockroom, to assist in the picking and packing process.
Label Source has a proven track record of supplying custom printed racking location identification labels for many warehouse projects. These can range from simple alpha-numeric labels, split beam labels (to identify a two location designation), and multi-location labels for beams or uprights (to eliminate the need for long range scanning).
Such labels for racks, shelving, or beams can be produced in a variety of materials. The most popular type is self adhesive synthetic materials, such as vinyl or polyester, with a protected surface laminate. These tear resistant labels are resistant to; water; abrasion; oils; cleaning solvents; and mild acids. Also, where there is a need to relocate stock positions, many customers opt for labels in magnetic material, which can be moved time and again without leaving any marks or residue.
If bar code scanning is required we can construct labels choosing from a selection of bar code symbologies, with the most popular being code 128, 3 of 9, interleaved 2 of 5, Data Matrix and QR codes.
So if you have an upcoming project on warehouse identification for bespoke racking labels, please contact us by e-mail (sales@labelsource.co.uk) or by telephone (0800 3761693 in UK, or +44 1443 842769 from outside the UK).
Other products available for marking racking or pigeon holes are; magnetic rack labels; ticket holders; and warehouse holders, magnetic or self adhesive).
An engineering firm in Hampshire has been fined £14 thousand (plus costs) over an incident that left one worker with a severed finger.
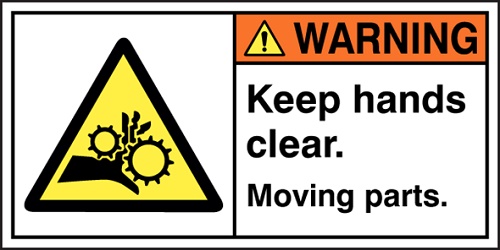
Pictured: 'WARNING: Keep hands clear. Moving parts.' safety label
Repro Engineering of Waterlooville (roughly 8 miles from Portsmouth) were ordered to pay up after an HSE inquiry concluded that the injury "could have been prevented by more active and robust management action". The incident in question occurred back in July 2015: the worker was trying to fix a jam in the lathe he was using when his hand came into contact with the machine's moving parts. He ended up losing a finger as a result.
This case was heard at Portsmouth Magistrates' Court, and Repro Engineering plead guilty to breaching Provision and Use of Work Equipment Regulations 1998*. Their primary offence was allowing access to the machine's moving parts while it was in operation, a very unsafe practice that sadly resulted in a rather gruesome accident.
Moving machine parts can be extremely dangerous, and this is why it's important to nurture safe working practices within any environment where they are present. Here at Label Source, we stock a variety of products that can help to prevent moving part accidents and remind workers of the risks associated with them:
*Specifically Regulation 11(1), which decrees that "every employer shall ensure that measures are taken...to prevent access to any dangerous part of machinery or to any rotating stock-bar [or] to stop the movement of any dangerous part of machinery or rotating stock-bar before any part of a person enters a danger zone".
Source: LRB Consulting