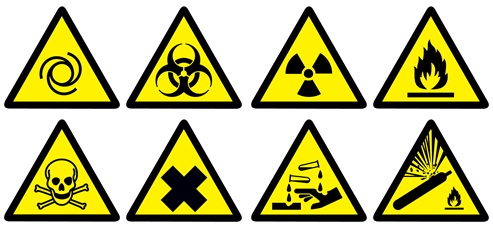
You probably see warning symbols like the ones pictured above practically every day. Granted, some people - such as those who work in labs or hospitals - will see them more often than others, but even if your job seldom exposes you to hazardous substances and situations, it's still important to know what these symbols mean. You never know when that knowledge might come in handy!
So how well do you know your warning symbols? Below, you'll find 10 standard warning symbols (all of which can be found in our Warning Symbol Labels department) - all you have to do is name the hazard that each symbol identifies. We bet you can't get them all!
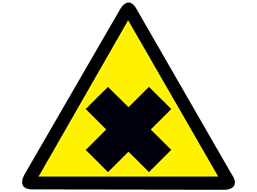
1) Can you guess what this big black cross means? Click here to find out!
2) This warning symbol is commonly seen in certain films and video games - if you don't already know what it means, find out here!
3) Come on - this one's easy, right? Answer here.
3) Reckon you know what this warning symbol means? Click here to find out whether or not you're correct.
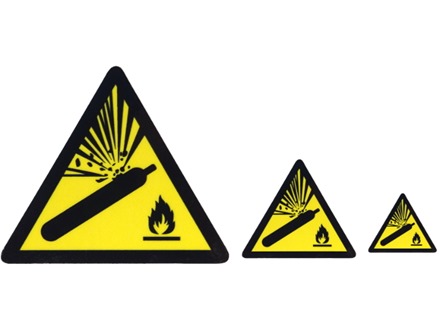
4) Exploding hot dogs? Something to do with cricket bats? Find out the true meaning of this symbol here.
5) Three wavy lines. What are they warning us about? Find out here.
6) Right, we've been going easy on you so far. Here's a tricky one - find out what it means here!
7) Confused? Click here to learn the meaning behind this assemblage of lines, arrows and fingers.
8) Slightly easier, this one - you've almost certainly seen it before, but what does it mean? Find out here.
9) More wavy lines! What do they mean? Answer here.
10) We'll end with a nice easy one. We're really hoping you know what this means - check your answer here!
So...how did you do?
0-3 points: Oh dear! Perhaps you need a warning symbol of your own?
4-7 points: Must try harder!
8-9 points: Good work!
10 points: Safety superstar!
Need to brush up your knowledge? Head over to our Warning Symbols department and do some revision for next time!