If you’re in a company that sends out a lot of parcels, you may be interested to learn that we stock a wide range of high-quality packaging labels. When sending out heavy, fragile, or multiple deliveries, it pays to inform the recipient exactly what they’re dealing with, so they avoid breakages, mishandling, or any other misdemeanours along the way.
Our packaging labels are seriously high quality – which is important, as if you are taking the time to inform users about your parcel, the last thing you want is a label that is easily damaged, or even worse, one that falls off!
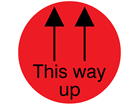
Luckily for you, at Label Source our packaging labels are all made using a self-adhesive vinyl – so take it from us, they’re not going anywhere. On top of that, we make sure that all of our labels are text-based, as even seemingly-obvious pictograms can sometimes be misleading. And as all of our labels come in rolls of 500 you’ll have plenty to go around.
If you like the cut of our jib, and you fancy bagging yourselves a reputable label supplier, Label Source is the name you have to remember!
When you need to mark hazardous goods or dangerous substances, to ensure safety in the workplace, and protection of the environment, choose from our extensive product range. Label Source has numerous, suitable health and safety signs and labels, complying with the latest legislation, international regulations and best practice.
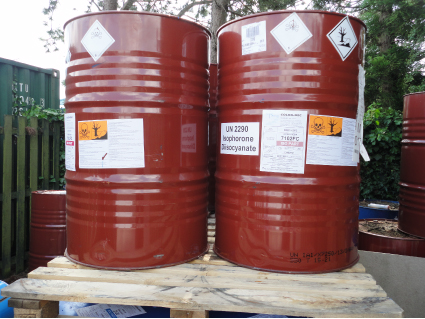
Whether you handle, process, store or transport hazardous materials in either solid, liquid or gaseous form, it is essential to clearly identify the contents, to protect workers, the emergency services and the general public.
Spills, incidents or accidents can result in injuries, ranging from minor to death, from explosions, fire and chemical burns from dangerous goods. These substances have been classified by the United Nations, and appear in a range of legislation including COSHH (Control of substances hazardous to health), GHS (Global harmonised system of classification) and CLP (Classifying, labelling and packaging regulations).
Therefore, our ranges of labels and signs are suitable for marking chemicals stored in bulk containers, pressure receptacles, tanks, drums, canisters and dispensing equipment, as well as production, storage and handling areas. Workers can be made aware of the risks from the hazardous goods and dangerous substances, such as toxic, corrosive, explosive, oxidising, flammable, irritants and hazards to human health and the environment.
At Label Source, we have a wide selection of custom labels that you can fully design yourself, and to your specific needs. We stock resin domed decals, coloured destructible labels, custom metal finish labels, custom high temperature labels, and customer write and seal labels – all of which can be fully customised, personalised, and tailored to your requirements.
As well as being visually effective, there is also a lot to be said about the remarkably high standard of quality of our custom labels. Our resin domed labels have a clear polyurethane lens for maximum visual impact, while also remaining scratch-resistant, shatterproof, and waterproof. Our custom metal finish labels on the other hand come in a mirror finish polyester, and are also scratch and chemical resistant, while retaining an eye-grabbing finish!
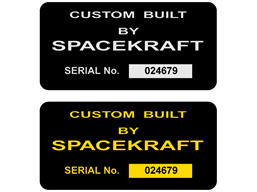
Basically, our labels are designed to withstand anything the workplace throws at them, without losing any of their striking visual appeal in the process. If you require custom labels to warn, inform, or brand your company, you will struggle to find a more reputable, high-quality vendor than Label Source.
As a facilities manager of any description, some of your primary roles will include health and safety, fire safety, security, and the maintenance, testing and inspection of your premises. For each of these roles you’re going to need the correct signs, labels, and tags to ensure the facilities you manage are safely maintained
Failure to meet health and safety requirements can lead to prosecution, insurance claims, loss of business, and of course injury. Luckily, at Label Source we sell a range of safety signs from hazard signs to mandatory safety signs, all of which ensure regulations are met by the general public.
When it comes it fire safety we can also assist facilities managers in their duties. Our fire equipment safety signs inform the public where all extinguishers, fire hose reels, and alarm call points are, making sure your area is fully protected in case of an outbreak of fire.
And of course when it comes to correctly labelling maintenance and testing items, we have your back fully covered! From plant maintenance labels to PAT testing labels, we sell only high-quality signs and tags that meet all the government regulations.
What’s been mentioned is literally only the tip of the iceberg, if you are a facilities manager and need help sourcing a vast array of quality labels, signs, and tags, come on over to Label Source and we’re certain we can assist!
We understand that for most of you the where’s, why’s and when’s of PAT testing can leave you feeling a little perplexed. Because of this, we have compiled a list of the most frequently asked questions and then answered them – because we can do a lot more than just offer you a selection of PAT testing labels, oh yes.
Should I Test My Portable Electrical Appliances Every Year?
The Electricity at Work Regulations act from 1989 states that any equipment with potential to inflict harm needs to be kept in a safe condition. It does not however specify what needs to be done, by whom, or indeed how frequently - so there is no legal obligation for annual inspection.
Should I test Any New Appliances?
As all new equipment should come fully tested and in a safe condition it should not require more than a visual examination. This means you should have no compulsion to purchase PAT testing labels from the go.
Should I Get a Qualified Electrician to Perform Any PAT Work I Need Done?
For basic PAT testing in low-risk environments, a sensible and competent member of staff can carry out inspections with the right training. When carrying out testing and inspection the member of staff will require the correct equipment and PAT testing labels, the ability to use such equipment, and the ability to correctly analyse the results.
Is it Compulsory to Conduct PAT Testing?
Simply put, no. What the law does state is that the employer knows electrical equipment is maintained in a safe order. The law also recommends taking a risk-based approach – think about the type of equipment, what it is being used for, and how often it is being used e.g. something in frequent use like a kettle may be a suitable candidate for PAT testing labels.