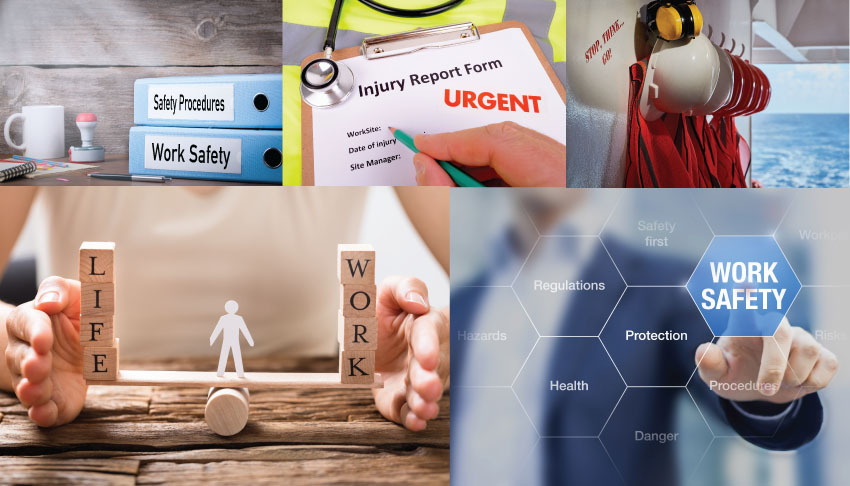
Having a goal of zero accidents is not only great from a safety perspective, but it’s also a helpful way of getting employees involved and making the safety of your workplace a collaborative effort.
The importance of accident prevention in the workplace is not one to be understated. The concept emphasises a proactive approach to the safety of your employees and others, as well as continuously learning and being able to identify new hazards as they arise. So, how can you create a zero-accident culture? These are our top tips on how to reduce workplace accidents.
10 Ways to Prevent Workplace Injuries
1. Risk Assessments
The first thing to do to minimise workplace injury is to conduct a risk assessment. This will help you identify risks both major and minor that you could encounter at work, and put you in a strong position to put in measures of avoidance.
For more information, have a look at our blog post on why it's important to have site-specific risk assessments.
2. Provide Adequate Training
Once you’ve identified the potential risks in the workplace, you must provide adequate safety training to all employees. This should be part of each employee’s induction into the workplace, and whenever a new risk is identified, all employees should be notified and re-trained depending on the risk level.
Conducting training regularly will help to keep the information fresh in people’s heads, ensuring that they don’t forget how to correctly respond to a risk after an extended period of time.
3. Supply Necessary PPE
For hazards that must be interacted with, such as handling chemicals or heavy machinery, the employer should provide employees with personal protective equipment (PPE) for any hazards they will regularly need to work around.
This might include steel-toe shoes, safety goggles, helmets, high-vis jackets or any other equipment that will improve the safety of an individual in your workplace.
4. Regular Equipment Maintenance
All machinery and equipment should be regularly inspected and maintained to minimise the risk of malfunctioning or causing an accident. The risk of equipment failure adds to the risk of injury, so ensuring that everything is always in prime working condition is paramount to employee safety.
5. Regular Safety Inspections
While your initial risk assessment will have identified many risks, there may be some that you don’t notice until the workplace is active. As well as this, most workplaces are constantly changing and evolving, so additional risks might come about over time.
For this reason, it’s important to carry out regular safety inspections to ensure that all risks are being acknowledged and addressed appropriately.
6. Encourage Reporting Close Shaves
Make sure your employees know it’s okay if a safety incident almost happens. Reporting these incidents alerts the necessary people of what needs to be improved for a safer environment, ensuring employees don’t come that close to an incident again.
It’s important to make sure workers know they won’t be reprimanded for coming close to an accident; reassure them that your workplace is an environment that encourages honesty and collaborative improvement.
7. Provide Supervision
Assign supervisors to oversee dangerous work activities. This will both reassure the team or individual carrying out the task and improve the response time if something does go wrong with someone designated to step in. Having multiple people around any particularly hazardous events will also help to correctly identify what exactly went wrong.
8. Encourage a Healthy Work-Life Balance
It’s important to recognise that things like fatigue and stress are also part of workplace safety. While they are dangers in their own right, being tired at work can also contribute to the risk of additional physical accidents and injuries.
Promoting a healthy work-life balance can reduce the risk of these things affecting your employees.
9. Continuous Improvement
Recognise the importance of staying vigilant on the potential risks in the workplace. Incentivise employees to report risks, and make sure that everyone is made aware of any newly identified hazards.
Keep on top of industry best practices and incident reports, and adapt your safety processes in line with the latest guidance.
10. Using Signage
Signposting and labelling all potential risks around the workplace will help remind people of any dangers as and when they encounter them. For example, placing PPE signs at the entrances to areas where it is required for PPE to be worn, using electrical warning tape on anything that could shock you, or fire safety signs that indicate where fire exits and fire safety equipment can be located.
Although regular training will help keep employees in the know, physical signage is an immediate and important reminder of any risks as they’re encountered.
Stay Safe with Label Source
We supply a vast range of safety signage for any situation. Properly signposting and health and safety risks will drastically improve the safety of your site, as well as helping you comply with HSE and government safety regulations.
Get in touch to find out about how we can help you, and keep up to date on the latest safety news on our blog.