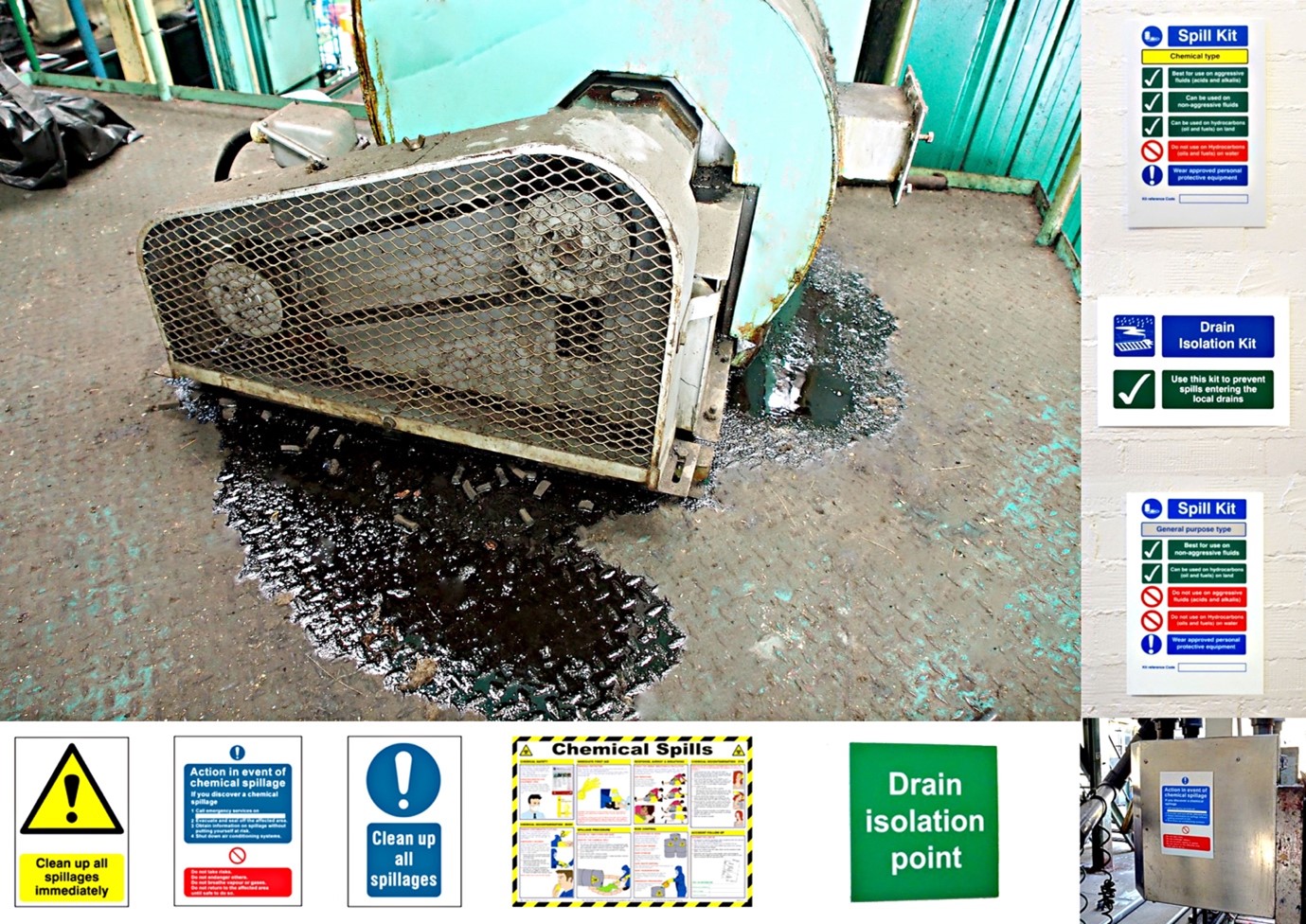
Spillages are common. Whether it’s a cup of coffee in the staff canteen or a serious spillage of stored liquids, both need some form of spill control to sort them out.
Without a spill control process, workplaces would find themselves culpable should a member of staff slip, and things get even more dangerous when we consider the storage of flammable liquids in warehouses.
To keep employees safe, employers must do two things:
- Establish a spill control protocol.
- Ensure liquids are safely stored to minimise the risk of spills happening.
Below, we’ll discuss how to store liquids safely, how to establish a spill control process and how signs can play an important role in both.
How To Safely Store Liquids
Safe storage of liquids depends on what type of liquid it is. Largely, liquids are categorised as flammable and non-flammable, and each has their own protocols to follow.
Flammable Liquids
Flammable liquids must be controlled in line with The Dangerous Substances and Explosive Atmospheres Regulations 2002. This law is in place to “control the risks to safety from fire, explosions and substances corrosive to metals.”
The law requires businesses to:
- Review and note which substances are dangerous in the workplace.
- Put measures in place to either remove or control the substance.
- Prepare a spill control plan that covers any ill effects from spillage, including damages to an employee’s health (both acute and long-term).
- Place hazardous material, including flammable liquids, away from any ignition sources.
- Train employees to handle the substance safely.
It is similar to the storage of gas cylinders, which we covered in our blog, Cooking on Gas: How to Ensure Gas Cylinder Safety.
You must ensure the storage of flammable liquids is done properly and these materials are kept away from ignition sources, but how do you do this? Overall, an employer should:
- Store the minimum amount of flammable liquid they need.
- Ideally, store the liquid on strong shelving.
- Ensure the storage area is well-ventilated.
- Review and remove ignition sources.
- Label the presence of flammable liquids so employees can take extra care.
- Refer to a spill control plan when accidents occur.
Non-Flammable Liquids
Non-flammable liquids have fewer risks than their flammable counterparts, but they can still be dangerous. Slipping on spillages is the number-one cause of workplace accidents, so controlling these can be key to keeping your employees safe.
Overall, to organise a workplace or warehouse, it’s recommended that an employer:
- Classifies, segregates and labels liquids by type and class. This helps with organisation and prevents incompatible liquids from mixing during a spill.
- Store at height, not on the floor. This requires excellent warehouse racking, as well as an efficient labelling system.
- Inspect the liquids frequently to check for leaks. Usually, a spillage does not happen at once, but builds up over time, especially in warehouses.
- Refer to a spill control plan when accidents occur and ensure those actioning the removal of spillages are trained.
How To Set Up A Spill Control Plan
A spill control plan will differ on a business-by-business basis. Naturally, a business that deals with chemicals will have a different spill control plan than, say, an oil refinery or farm. However, all spill control plans must cover the following:
- A risk assessment. This should be the first step to any spill control plan, as it dictates the entire response.
- A list of PPE and where to find them in the business. This is especially important when accessing hazardous material.
- Methods to confine the spill. This can be done using various methods, from specialised powders to signs.
- Methods to stop the spill at the source.
- A full decontamination plan.
- A plan to clean and dry the affected area. Too often, this step is neglected, leading to slippages.
Overall, by setting up a spill control plan, businesses can be prepared for any type of spillage in the workplace.
In-Process Spills
As part of a spill control plan, you also need to consider in-process spills. This is when a spill is happening over time, but it can't be stopped immediately.
To combat this, ensure you use the correct labels to inform staff that a spill is occurring and signpost around it. If the spill is of a chemical nature, then use the directions around the element to ascertain what protocols you should put in place.
Buy Spill Control & Liquid Storage Signs Today
To help you identify liquids and spillages, consider our range of spill control and liquid storage signs. These help to control everything from chemical spills in the workplace to the most basic liquids.
Plus, when you buy from Label Source, you’re buying from a brand with a hallmark of label quality.