The construction industry is getting to grips with The Construction (Design and Management) Regulations 2015 (CDM), which came into force on the 6th April 2015. The aim is to improve the health and safety record within the construction sector, thus leading to a reduction in the number of accidents, and as a consequence less serious injuries and fatalities.
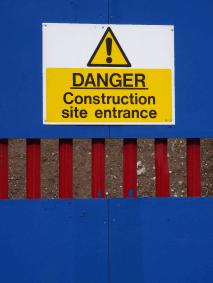
The regulations have a very wide remit, and the intention is to streamline the construction process between designers, main contractors and sub-contractors, so that there are less ‘grey areas’ of responsibility and clear lines of demarkation, with the promotion of health, safety and welfare. This includes the managing of risk, with emphasis on the co-ordination of work, suitable appropriate training, use of suitable skilled staff and the means of communication.
The remit of these regulations cover the planning, management, monitoring and co-ordination in construction and building refurbishment of commercial, industrial, retail and domestic projects, including site preparation and demolition. It includes the following aspects;
Fall from heights, including use of ladders, platforms, scaffolding, towers, and fragile roofs.
The use of support systems to prevent collapse of excavations or building structures.
Exposure to airborne particles and fumes, with inhalation of dust, lime, lead , asbestos or from vehicle diesel exhaust.
Electrical hazards from electrical systems in buildings, overhead or buried power lines.
Slips, trips and falls on uneven surfaces, alterations in levels, trailing wires, obstacles or wet or slippery floor surfaces.
Fire hazards for the safe storage of combustible materials and control of sources of ignition, including fire training on escape routes, assembly or muster points, or the location of fire fighting equipment.
Safe operation of cranes.
Safe operation of mobile plant and vehicles, including excavators, mobile work platforms, dumper trucks and road vehicles.
Site traffic control, and the prevention of entry to unauthorised persons, including the general public, and in particular children. Also, this covers car parking, site speed restrictions, and deliveries.
Housekeeping of materials storage, and management of waste (skips, wheelie bins, chutes).
Control of hazardous substances and dangerous chemicals.
Protection against physical hazards, such as noise, vibration through use of power tools, manual handling and repetitive strain.
Employee welfare, such as toilet, wash, rest facilities, and first aid.
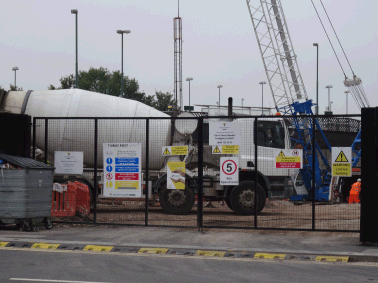
Label Source can assist you in meeting your obligations by supplying health and safety labels and signs to the latest legislation for CDM applications, to highlight operational dangers and hazards, prohibited activities, mandatory actions (including the use of personal protective equipment supplied), and safe operating conditions. These can be used in your induction and training activities for site specific activities, so that all employees are suited to their roles in a safe working environment. Also see our ranges of tapes and barrier mesh for use on building sites and work excavations.